Finishing in Printing: What are the Most Requested Options?
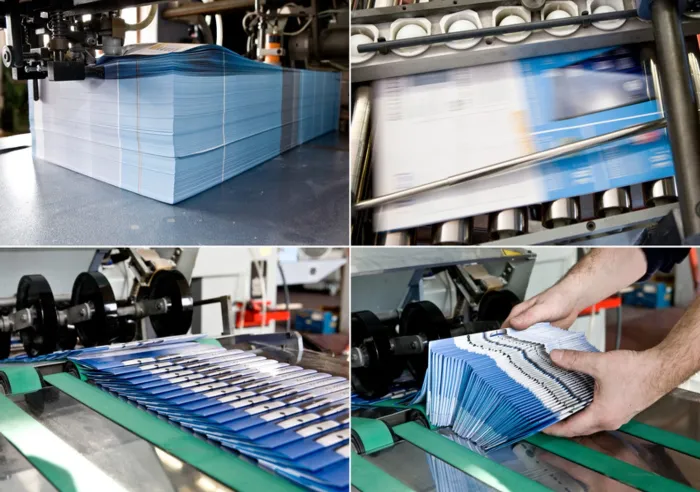
estimated reading time: 10 minutes
Finishing Options for Printing
In the realm of printing, the term "Finishing" refers to the
various processes and enhancements that a print project might undergo after the
ink has been applied to the paper. Finishing adds value to a print project by improving
its appearance, durability, and/or functionality.
Below is an alphabetized list of the most popular and often
requested finishing options…
Aqueous Coating -
Aqueous Coating is an economical clear coat that helps
printed pieces resist minor scuffs and scratches. As its name signifies, aqueous
coating is water-based. When applied over a printed substrate, it disperses water-soluble
polymers onto the surface. These polymers form a protective film over the
printing as the water evaporates. Aqueous coatings are available with a gloss,
matte, or soft touch finish. Aqueous coatings can only be applied as a flood coat and work
best for projects printed on coated stocks. Though aqueous coatings add some
resilience to printed pieces, they are not as durable as UV coatings or
laminates.
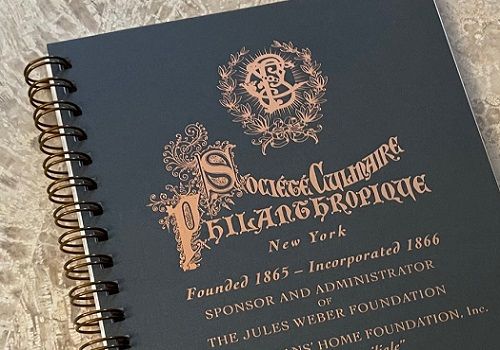
Binding -
Binding refers to the process of fastening multiple sheets
together. Binding is most often associated with book creation, where the cover
and pages of a book are joined together using adhesives, stitching, or various mechanical
means such as staples or binding coils. Ringed binders, such as the widely used
3-ring binders, are another popular way to securely bind pages together. Also,
printed cards, such as those used for quick reference or educational purposes, are
often bound into convenient sets using a screw-and-post system or by inserting
a metal ring through a hole punched in each card.
Collating -
Collating refers to the process of collecting and assembling
printed sheets in a specific order. Many print projects, including books and
brochures, require multiple printed sheets to be arranged in a pre-determined
sequence. This results in sets of printed sheets that are organized in a
consistent and logical manner. Though some projects are occasionally collated
by hand, the majority of projects use automation to perform the collation of
printed documents.
Cutting and Trimming -
More often than not, the Cutting and Trimming process is an
essential step in print production rather than being an optional request. This
is because many projects are printed multiple-up on a parent sheet and then
separated into individual pieces using a cutting blade or shear. In addition to
cutting larger sheets into smaller pieces, trimming operations are used to
remove excess paper from the perimeter of printed pieces. Both methods reduce
the physical size of a printed sheet to yield the desired finished size.
Die Cutting -
Die Cutting refers to a creative fabrication technique that
cuts paper, cardstock, label stock, and other substrates into shapes that
cannot be achieved with straight-line cutting. Functioning much like cookie
cutters, cutting dies have thin metal blades formed to match the outline of the
desired shape. The sharp die is then pressed into the printed stock, cutting
the substrate into the new shape. In addition to giving printed pieces a more
interesting contour, die cutting can also add features that make printed pieces
more functional, such as hooks for door hangers, business card slits for
presentation folders, interlocking flaps for packaging, and so on.
Drilling -
Drilling uses a rotating bit to bore round holes in paper
and other substrates. Drilling is efficient because it can bore through large
stacks of paper, creating clean holes in hundreds of sheets at once. One of the
more common uses of drilling is adding holes to the sheets and tabbed dividers that
will be placed in a ringed binder, such as the popular 3-ring binder. Drilling
is also used to create the round holes that give certain printed pieces the ability
to suspend from something, such as wall calendars or hang tags.
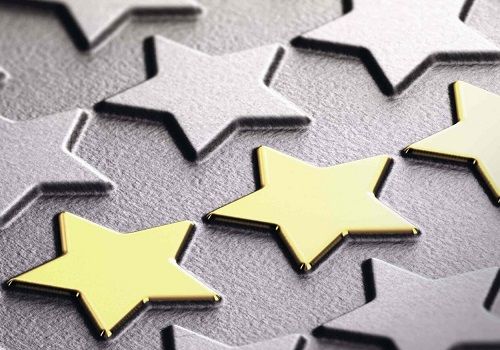
Embossing and Debossing -
The finishing techniques of Embossing and Debossing add
a three-dimensional effect to paper and cardstock. Both the embossing and
debossing processes use a matched set of metal dies - one male and one female. The
substrate is placed between the two mating parts and, with the aid of pressure
and heat, the dies press logos, text, shapes, or patterns into the paper substrate.
The difference between embossing and debossing is the direction in which the
image is pressed into the paper. Embossing creates a raised design whereas debossing
results in a recessed design. Both methods cause the paper or cardstock to permanently
conform to the shape, enhancing visual appeal and drawing attention to the
printed piece. Embossing and debossing can be used as standalone techniques or
in combination with spot clear coats, colored inks, or metallic foils.
Foil Stamping -
Foil Stamping involves the transfer of a metallic or colored foil to specific areas of a paper or cardstock substrate. A custom-made die applies the foil using heat and pressure. The foil, which is applied in the shape of a logo, tagline, text, or other design exhibits high reflectivity and gives a very high-end look to book covers, brochures, business cards, and other pieces intended to make a positive impression. In addition to popular metallic finishes like gold, silver, or copper, foils are available in a variety of striking colors. Holographic effects can also be achieved with foil stamping. Furthermore, this distinctive finishing method can be used by itself or combined with the embossing technique.
Folding -
Folding is a very common finishing step. A fold
involves bending one part of a printed piece back upon itself until it lies flat.
Folding can be incorporated to reduce the overall size of a printed piece and/or
enhance its functionality. As such, folding is a critical part of many print
projects. For example, saddle-stitched booklets and catalogs are created
entirely of folded sheets that are bound together with wire staples. Also, many
popular types of brochures and pamphlets, such as the bi-fold, tri-fold, and
accordion fold are created simply by using different folding sequences. It's
also no secret that the majority of menus and maps are folded to make them more
convenient to use. Most print materials, especially those produced in volume,
are folded with specialized machines that can fold precisely (and pre-score if
necessary) to ensure a clean and professional appearance.
Laminating -
Many print projects have an optional clear Laminate applied
as a finishing step. Made of durable plastic film, laminates are bonded over printed
pieces to add a layer of protection. In addition to guarding against damage
from dirt and moisture, laminates help the printing resist scuffs and wrinkles.
Plus, laminated printing is nearly impossible to tear. Available in various
thicknesses, textures, and sheen levels, laminates offer a practical way to
improve the look, function, and longevity of printed items. Printed items that
are handled frequently and/or subject to stains and spills are often ordered
with a laminate. Common examples include restaurant menus, placemats and
counter mats, training materials, flip books, reference sheets, cards and tags,
book covers, brochures and marketing pieces, bookmarks, and business cards.
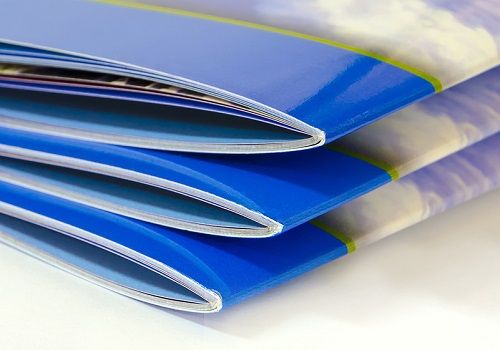
Padding -
Many business documents are made into multi-sheet Pads.
Common examples include handwritten forms, expense reports, memos, picking
slips, and checklists. After the printed sheets are assembled into a neat stack,
a flexible adhesive is spread over one edge of the stack. The adhesive tacks
the sheets together but allows the topmost sheet to be easily removed while the
remaining sheets stay attached as a unit. A chipboard backer is normally attached
to the bottom of the stack to provide rigidity to the pad. Multi-part
carbonless NCR forms can also be created as convenient pads. Pads of NCR forms
often have a stiff cover that can wrap around the stack. This cover can slide
between the topmost form and the one below it to act as a backer sheet, thus preventing
any unwanted transfer of handwritten data to subsequent forms in the pad. If
desired, padded documents can be printed with sequential numbers, allowing each
sheet within the pad to have a unique identification number.
Perforating -
In the printing industry, Perforating refers to the process
of creating a series of tiny holes or slits in a sheet of paper, cardstock, or other
substrate. The perforation line allows for a portion of the printed piece to be
torn away by hand without harming the base substrate or the section that was
removed. Most perforations are created in a straight line but occasionally a print
project will require a curved perforation. The size of the punched holes (or
slits) and the amount of space between them is what determines how much force
is needed to separate the perforation and how clean the tear line will be.
Small, closely spaced holes will result in an easier and cleaner-looking tear,
whereas larger and/or further-spaced holes require more pull force and will leave
a rougher edge. Some examples of print projects that use perforations include
marketing door hangers with a detachable business card and promotional mailers
or postcards that have a removable coupon or response card. Perforations are
also sometimes used to separate printed pieces from each other, such as raffle
tickets or continuous NCR forms, or to separate them from a main stub, such as
checks or receipts.
Punching -
Punching is somewhat similar to drilling in that it creates
holes. However, punching involves forcing a sharp die through a substrate
rather than using a rotating cutter to bore through it. Though a paper drill
can penetrate a thick stack of sheets, a paper punch cannot penetrate as many sheets
at one time. However, where a drill is limited to creating round holes, a punch
can make holes of various shapes and configurations, such as the elongated
holes used for lanyard straps or the sombrero holes needed for product header
cards. Punches are also used extensively for making many holes at once, such as
the series of holes or slots needed for a book's cover and pages to accept a
spiral coil, wire-o, or comb binding spine.
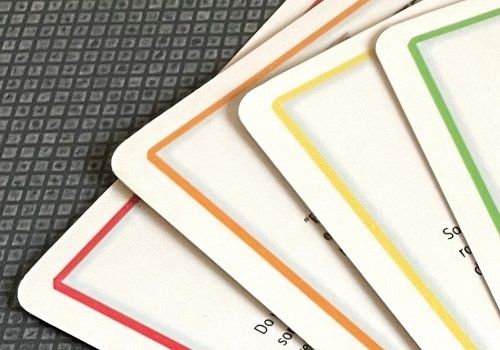
Round Cornering -
Round Cornering in printing refers to the process of adding
a radius to the square corners of print materials, such as business cards, reference
sheets, flashcards, hang tags, bookmarks, menus, books and booklets. Rounded
corners provide a polished look, which can boost the aesthetic appeal of many
print materials. Also, unlike a traditional square corner, the curvature of a
rounded corner helps deflect the stress on any single point. This reduces the
risk of the corners become prematurely dog-eared and frayed. Rounded corners
are also highly recommended whenever a printed piece has a thick laminate
applied. Due to the rigidity of thicker laminates, square corners can become
quite sharp. This creates a safety hazard, especially when the laminated
materials will be handled frequently and/or used by young children. Round
cornering is a popular option for business cards, hang tags, flashcards,
children's books, field guides, and reference sheets.
Scoring -
In printing, Scoring refers to making a crease or slight
indentation in paper or cardstock so that it folds cleanly. Scoring is
particularly important when preparing to fold heavyweight papers and cardstocks.
Without scoring these heavier stocks beforehand, they will not fold smoothly.
Buckling of the stock or splintering of the paper fibers will likely occur. The
scoring procedure uses a rigid scoring wheel or metal rule that presses into
the paper, forming an indention that slightly weakens the paper and makes it
more pliable along the intended fold line. Scoring is commonly used in the
production of presentation folders, greeting cards, invitations, note cards,
the covers of books and booklets, thicker brochures, restaurant menus, table
tents, fold-over business cards and any other print project that requires the
folding of heavier papers or cardstocks.
Sequential Numbering -
Sequential Numbering refers to the printing of numbers,
in consecutive order, onto a batch of printed pieces. Every printed piece
within the batch receives a different number, allowing each piece to be
uniquely identified. The numbering process can begin at any chosen number and the
numbers can be printed in ascending or descending order. However, ascending
order is by far the most widely used format. Also, the numbers can be printed in
a single location on each piece, or in several locations on each piece. In
addition, sequential numbers are often printed in red ink to make them more
prominent. Sequential numbers provide quick identification and accessibility,
saving time and effort while categorizing, filing, or retrieving printed
documents. Equally important, sequential numbers allow each piece to be
individually accounted for, ensuring there is no replication or unauthorized
use.
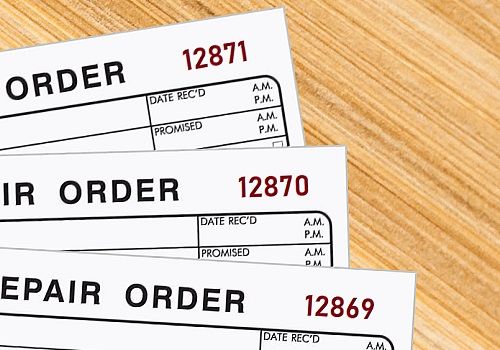
UV Coating -
UV Coating is a hard-wearing clear coat that enhances
the durability and appearance of print materials. Made of polymer resin, UV
Coatings are applied in liquid form and dried by exposure to Ultraviolet (UV)
light. The UV light hardens the coating in a matter of milliseconds. UV
coatings can be flood coated over an entire piece or applied as a spot coat to
specific areas. Though not as tough as a laminate film, a UV coating offers
incredible resistance to scratches and abrasions. UV Coatings are available in
a variety of textures and sheen levels, including gloss, matte, and soft-touch.
Gloss UV is by far the most requested UV coating option. It adds a
glass-like shine and slick feel to printed pieces. In addition to adding a
layer of protection, a gloss UV makes ink colors more vibrant. This added
vibrancy makes gloss UV a popular choice for full-color projects, especially those used for marketing and promotional purposes.
Yes, Color Vision offers all of the Finishing Options listed above!
As a full-service printing company, Color Vision has an
extensive finishing and bindery department. In addition to offering all of the
finishing options outlined above, we have a wide selection of binding styles
for your book and booklet projects.
So if you are looking for creative and affordable ways to enhance
your print materials, give us a call at 800-543-6299 and we'll be happy to
discuss ideas with you.
Or, if you already know your project's specs and would like
a price quote, just fill out our easy Quote Request form and we will be glad to
prepare a custom quote for you.
As always, we hope to hear from you soon and
look forward to assisting with your printing and finishing needs!
Related Articles
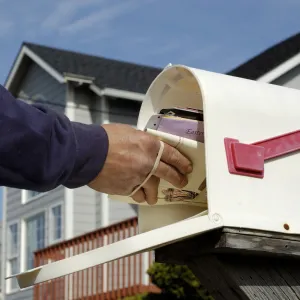
Direct Mail Marketing Campaigns: 3 Different Approaches
Read This Article
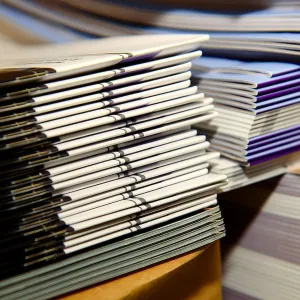
How Print Materials Help a Business Accomplish its Goals
Read This Article
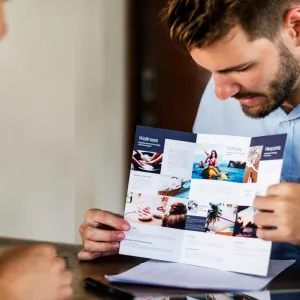
Print Marketing: 5 Low Cost Ways to Promote your Business
Read This Article
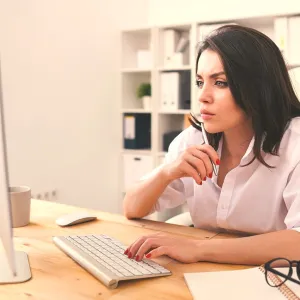
Printing Proofs: Pay Extra Attention to Contact Information
Read This Article