Custom Comic Book Printing: 10 Frequently Asked Questions
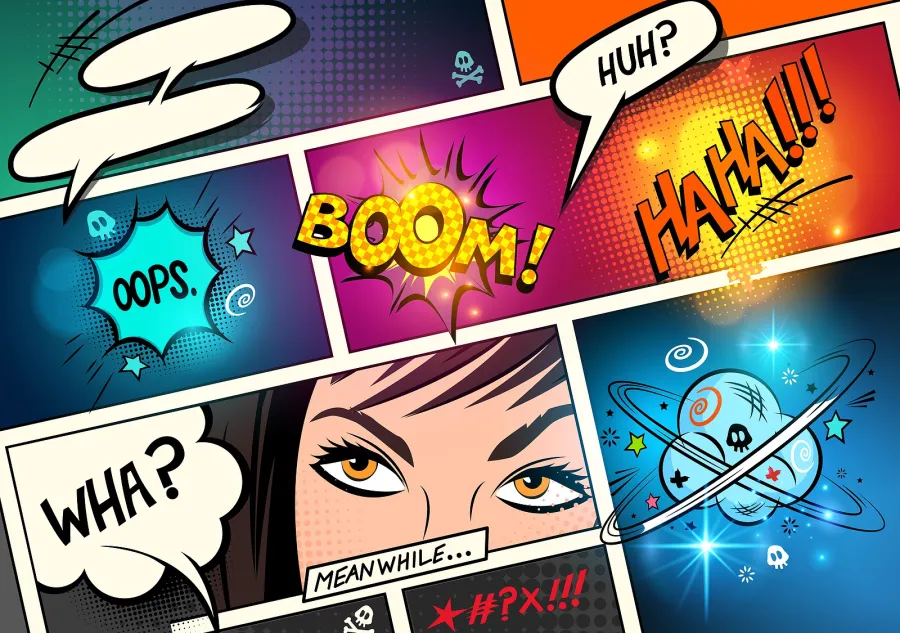
estimated reading time: 10 minutes
Custom Comic Book Printing
Whether you are a new comic book creator or have already built
a loyal following, you probably know that professional printing is a powerful
way to boost the credibility of your creative projects.
Even though the computer age has brought about a shift toward digital versions of comics, there is still something special about
holding a printed comic book in one's hands. Whether it's for the nostalgia, or
because a physical copy involves more of our senses, many readers find printed
comics provide a more immersive and satisfying reading experience than a
digital format.
So if you are planning to have comic books produced in the physical
form of ink on paper, you probably have some questions about the available
printing options. That said, below are answers to 10 questions that are
frequently asked about custom comic book printing…
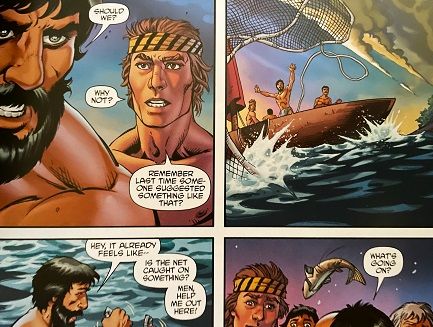
1. What Binding Options are available?
Since the Golden Age of comic books, Saddle Stitch
Binding and Perfect Binding have been the two most prevalent binding
methods for comics.
Saddle Stitching is the binding style most commonly used for
thinner comic books. It is the binding style most people associate with a
traditional comic book. It is also the most economical binding style.
With this method, printed sheets are folded and nested
together. Wire staples are then driven through the fold line from the exterior
and cinched closed within the centermost pages.
With the saddle stitch method, each folded sheet creates
four pages of the comic book. Therefore, the page count of saddle stitched
comics must always be a multiple of four, e.g. 24 pages, 32 pages, 48
pages.
With respect to Perfect Binding, it is the binding style most commonly used for
thicker comic books. The perfect binding process involves gluing a stack of
printed pages within a durable wraparound cover. Once the glue cures, the books
are trimmed along the three open sides to create edges that are clean and
straight.
The perfect binding method produces a flat spine which can
be printed upon. Perfect binding costs a little more than saddle stitching but
it is still a relatively economical binding choice.
Comic books can be made with other binding styles like
Hardcover Binding, or punch and bind methods such as Spiral Coil or Wire-O
binding. However, these binding methods are not considered a mainstream choice
for comics and are generally reserved for special editions.
2. What types of Paper are available?
The thickness, texture, and finish of the paper you choose will
have a big impact on the appearance and feel of your comic book. Though some
printers only have a limited paper selection, a totally custom printer will be
able to produce your comics on any type or weight of paper you choose.
The two primary classifications of paper are Coated and
Uncoated. Gloss Coated stocks have a slick and shiny finish that will make ink
colors appear more vibrant. Gloss coated stocks are great for showcasing full-color
and action-oriented artwork. Matte Coated stocks have a smooth but minimally
reflective finish. Colors appear softer on a matte stock and text-heavy comics
are easier to read because of the reduced glare.
Uncoated stocks offer a rougher texture with a more natural
paper feel, much like the pages of vintage comics. Ink colors will appear somewhat
subdued on an uncoated stock but the natural paper texture offers a more
tactile experience.
Regarding the thickness of paper used for custom comic
books, there are lighter text weights and heavier cover weights from which to
choose. The most popular options for the interior pages include the text weights of 60 lb, 70 lb,
or 80 lb. Cover weights range from 80 lb to 130 lb, with the heavier weights
usually reserved for the covers of comic books made with the perfect binding
method.
3. What are the Ink Color options?
Commercial printing companies typically offer the following ink
color options:
CMYK (Cyan, Magenta, Yellow, Black ink colors): also known
as 4-color process printing, CMYK is the industry standard for full color
commercial printing. Combining the four CMYK inks in various concentrations can
create about 16,000 different colors. CMYK produces vibrant and high-quality
images, so it is a must for color-intensive covers and pages.
Grayscale / Black and White: these economical color modes use only
black ink. Grayscale uses black ink in varying intensities to create images in
shades of gray. Black and White printing uses black ink at 100% to form
contrast with the white paper substrate. Many comics print in these color
modes, especially if they have a dark, scary, or mysterious theme. Grayscale is
also a popular color mode for the pages of graphic novels.
PMS Spot Colors (Pantone Matching System): PMS inks are
specific color formulations that cannot be exactly replicated with the CMYK
inks. There are about 2,000 PMS colors, including metallic and fluorescent
inks. Offset presses can print every PMS ink color. There are also Digital
presses that can print some of the exact PMS colors.
4. What is the "Self Cover" option?
Many comic books are ordered with a cover that is slightly
thicker than the paper used for the inside pages. Other comic books are ordered
with the "Self Cover" option. Self Cover simply means the same paper
stock is used to create the entire book. In other words, the exterior cover and
interior pages are printed on the exact same type and weight of paper. For example,
70# gloss text throughout.
The cover could be a lighter weight to match the pages, or
the pages could be a heavier weight to match the cover. Either way, the
self-cover option provides some cost savings because the entire book can be
printed and assembled all at once, as opposed to requiring two separate
production runs for the cover and pages.
Technically, any softcover binding style can be used in
conjunction with the self-cover option. However, saddle-stitching is the
binding method most frequently used to create self-cover books.
5. What is the most popular Comic Book Size?
The most popular finished size for comic books is 6.625" x
10.25". This is considered the standard size for modern comics. Other common
sizes include the 5.5" x 8.5" digest size and the 8.5" x 11" magazine size.
Some printers also offer custom sizes, which means you can
request any size or orientation you want as long as it is a practical fit for
your preferred binding style.
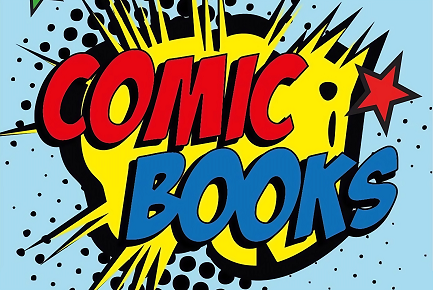
6. What can I do to set my Comic Book apart?
If you want your comic book to have a truly unique
appearance, find a printer that has an extensive finishing department.
Finishing refers to various customization options that can be added after the
ink has been applied to the paper.
Below are examples of finishing operations that will enhance
the appearance of your comic book and help set it apart…
Foil Stamping: The foil stamping process applies metallic
accents to the cover, producing a stunning optical effect. Foil is available in
various colors as well as popular metallic finishes like gold, silver, or
copper.
Spot UV: A gloss Spot UV coating can be used to highlight
specific areas of the cover artwork by giving these areas a higher sheen level
than the surrounding surface.
Embossing/Debossing: Embossing creates a raised design and
debossing creates a recessed design. Both methods create a 3-dimensional
effect. The paper substrate is placed between two mating die sections and then
heat and pressure is applied to permanently elevate or indent the design. Embossing
can be used in conjunction with Foil Stamping or Spot UV.
Die-Cutting: As the name
implies, die-cutting refers to a method of cutting shapes into
paper, cardstock, and other substrates using a sharp metal die. The
die-cutting process is used to add sculpted edges, rounded corners, see-thru
"windows", and interesting patterns and contours.
Soft Touch Finishes: A soft touch finish appeals
to the sense of touch by providing a velvety or suede-like feel. This finish is
achieved either by using a liquid coating that yields a soft-touch texture as
it dries or by applying a soft touch laminate film. The unusual texture adds
intrigue and heightens the reader's interaction with the cover and/or pages.
7. What's the deal with Variant Covers?
A Variant Cover refers to cover artwork that is different
from a comic book's primary cover. For example, a comic creator might place an
order with a printing company for a total of 1000 comic books, where 850 are to
be made with the primary cover (Cover A), 100 are to be made with variant Cover
B, and 50 are to be made with variant Cover C.
The cover art varies but the interior pages remain the same for all 1000
books.
The artwork used for variant covers is often created by
different artists. Variant covers are sometimes produced to commemorate an
event, or as an exclusive offering at a convention or through a reseller. In
addition to displaying different artwork, variant covers might also create
distinction with foil stamping, embossing, spot UV, or other enhancements.
Variant covers are intentionally printed in limited numbers
to create scarcity, with the goal of making them more appealing to collectors and
die-hard fans. Because variant covers are produced in smaller runs, the printing
and assembly costs will be slightly more per unit than the main run. However,
this will be more than offset by the higher price consumers are often willing
to pay for editions with variant covers.
8. Is there usually a Minimum Order Quantity?
You will find that the Minimum Order Quantity (MOQ) varies
from printer to printer. For example, a printer that specializes in On-Demand
printing may have a minimum order quantity as low as 1-10 books. Traditional digital
printers usually have minimums in the range of 25 to 300 books. Printers that
only have offset presses will have higher minimums for production, likely 500
to 1000 books. This is because an offset press is not cost-effective when
producing lower quantities. However, offset printing is by far the best value
when printing in higher quantities.
Regardless of the production method, the unit cost will always
be higher at lower production quantities and lower at higher production quantities.
Having said that, it is recommended that new comic book launches start off using
digital printing services. Then as the demand increases, the orders should switch to
offset printing to take advantage of the economies of scale. You will be amazed
how much offset printing will decrease the unit cost at higher production volumes.
9. What File Format should I submit?
Almost all printing companies prefer that your artwork files be submitted as high-resolution PDFs. Also, to maintain print quality, images and artwork should be at least 300 dpi. Color mode should be CMYK, not RGB. If using PMS spot colors, be sure to specify the Pantone numbers. Bleed should extend 0.125" beyond the trim edge and crop marks should be properly placed. Additional recommendations for file submissions can be found here: How to Submit Artwork
10. What should I consider when Choosing a Printer?
Naturally, you will want to select a printing company that
consistently produces high-quality printing. Requesting samples of comic books
they have printed will help you gauge the quality level first hand. Also, if
possible, check with other comic book creators to learn about their experiences
with the quality, pricing structure, and turnaround times of the printer you
are considering.
In addition, choose a printer that has the equipment and
capabilities to meet your specific printing requirements. As mentioned earlier, digital
presses are ideal for producing short runs of books and offset presses are
better for larger runs. Finding a printer with both types of presses is a major
plus because it will allow your comic book to be economically produced at lower
quantities initially as well as at higher order quantities when the demand for your
books increases.
It is also important to research how long the printer has
been in business. Longevity is a reliable indicator of success because it
demonstrates that customer satisfaction has been sustained over time. Printing
companies that prioritize long-term client relationships are the ones most
likely to have a strong foundation in place, thus enabling them to meet your
needs well into the future.
Other vitally important requirements for a printing company
are first-rate customer service and excellent communication skills. You want to
select a company that not only meets your printing requirements but also takes
an interest in your project, is helpful and responsive, provides clear
explanations, and works hard to help you achieve your goals.
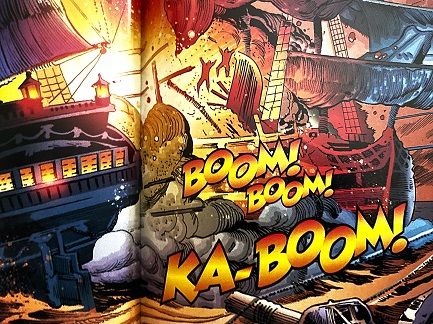
Color Vision is your Totally Custom Printer!
Color Vision specializes in book printing and has been
printing custom comic books for over 40 years. As a full-service print
facility, we have both digital and offset production capabilities. This allows
us to meet the needs of independent comic book creators as well as publishers.
Being a totally custom printer, we can produce your comic
books with any ink colors, paper type, physical dimensions, binding style, or genre you desire. We also offer a wide variety of finishing options to make your
comics unique.
Just give us a call at 800-543-6299 to discuss
your project. Or, use our simple Quote Request form to send us your
specs and we'll be happy to email a custom quote to you.
Custom comic book printing is a rewarding process that
brings your creative vision to life, so we look forward to assisting with your upcoming projects. Just let us know how we can be of service!
Reasons to Buy your Comic Books from Color Vision Printing…
- You will communicate with Real People who are eager to offer
help and guidance
- We are a Totally Custom Printer - your options are virtually
unlimited
- We have Digital and Offset presses to accommodate varying
run sizes
- Extensive Selection of Finishing and Binding Options
- Friendly and Helpful Staff dedicated to your Success
- 40+ Years in the Printing Business
- All Books are printed in the USA
- Excellent Quality and Prices
- A+ BBB Rating
Related Articles
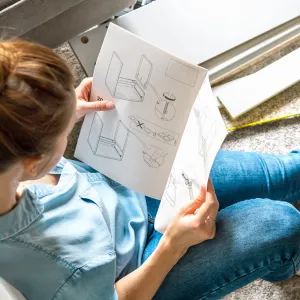
Why is a “Self Cover” Booklet more Economical?
Read This Article
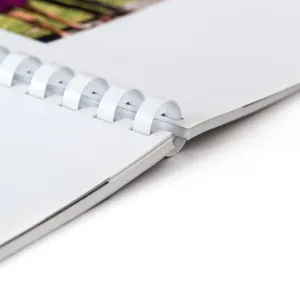
Plastic Comb Books: What does the "Comb" refer to?
Read This Article
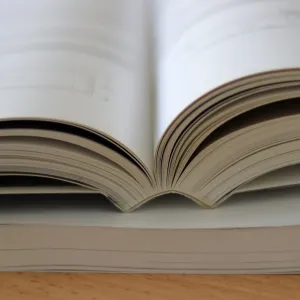
The Benefits of PUR Binding
Read This Article
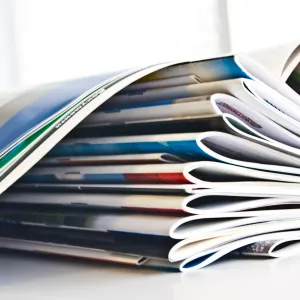
What is the Best Page Count for Saddle Stitch Binding?
Read This Article