Comic Book Binding: Exploring the Two Most Popular Methods
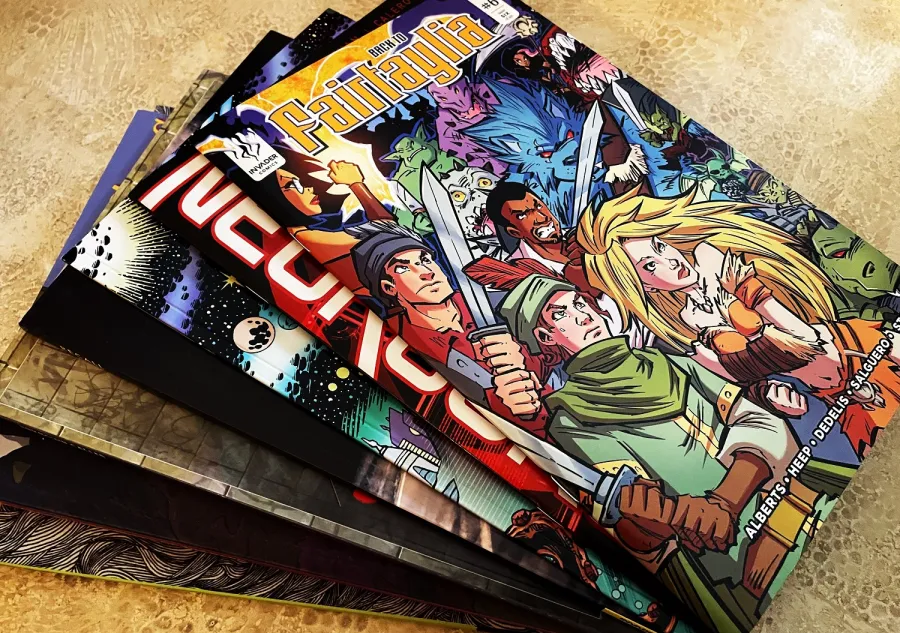
estimated reading time: 5 minutes
Since the Golden Age of comic books, two binding methods
have remained at the forefront - Saddle Stitch Binding and Perfect Binding. Though
these two methods have vastly different production processes, both provide a
practical and economical binding solution for a variety of comic book formats.
To help you determine which of these binding methods is a
better fit for your particular project, we have provided a detailed
explanation of each method below…
Saddle Stitch Binding
The Saddle-Stitch Binding process uses wire staples to join a
comic book's cover and pages together. After the page sheets have been
printed, they are partially folded and then draped over a saddle-like apparatus.
The page sheets nest together as each falls into place. Each folded
sheet creates four pages of the comic book.
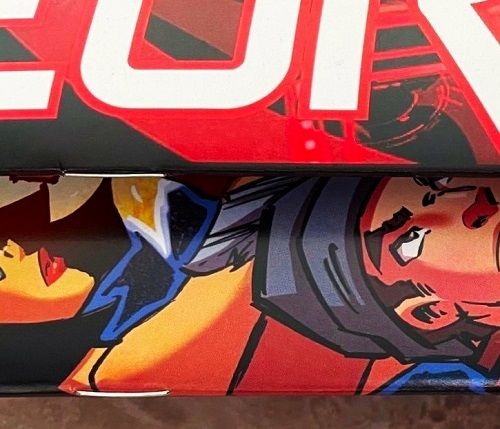
After all the folded page sheets have been compiled in the proper
order, a folded cover sheet is applied over the page assembly. Several wire
staples (usually two) are then driven through the fold line of the assembled
sheets. The staples first penetrate the outside cover, then pass through every
interior sheet until they pierce the innermost sheet.
The staples are then cinched closed in the fold line of the
innermost sheet. The staples hold the pages and cover tightly together, while
allowing the pages and cover to turn freely. The stapled fold line of the
assembly forms the book's spine.
The crown of each staple remains visible on the exterior of
the book's spine and the bent legs of the staples are visible in the fold line
of the book's center spread. After the book has been stapled, it is folded tighter together and the open edges of
the book are trimmed as needed.
It should be noted that saddle-stitching works best for
comics with lower pages counts. This is because wire staples can only secure a given
number of pages. Trying to bind too many pages with staples can create excessive bulk and tension near the spine. This leads to a bulging effect that prevents the book from lying flat. So, our recommendation is to only use the
saddle-stitch method to bind a maximum of 60 pages if you prefer a nice flat
comic.
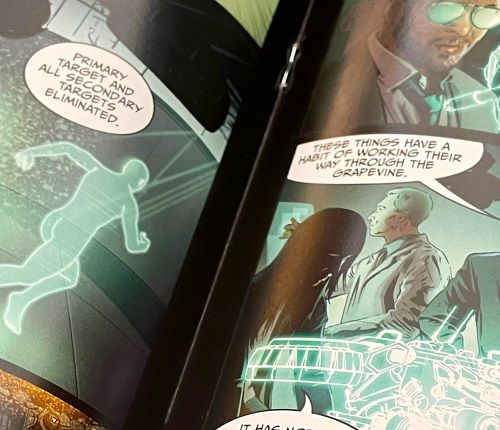
When most people think of a traditional comic book, they
tend to think of a thinner book made with saddle-stitched construction. Because the majority of comics do have a relatively low page count, they also have limited rigidity. Hence, thinner comic books are commonly referred to as
"floppies."
Regarding the cost, saddle-stitching is the absolute
cheapest binding method available. Despite its low cost, it produces securely
bound and professional-looking comic books. This helps explain why, decade
after decade, saddle stitching has remained the most prevalent style of comic book
binding.
Perfect Binding
Unlike saddle-stitching, which uses a mechanical fastening
method, the Perfect Binding process uses a special hot-melt adhesive to secure
the pages into a wraparound cover. The adhesive provides a strong bond but remains
flexible after it has cured.
The perfect binding process is slightly more involved than
the saddle-stitching process. After the pages of the comic book have been
printed, they are collated into a compact stack. This stack is known as the
page block. Each sheet within the block creates two pages of the book.
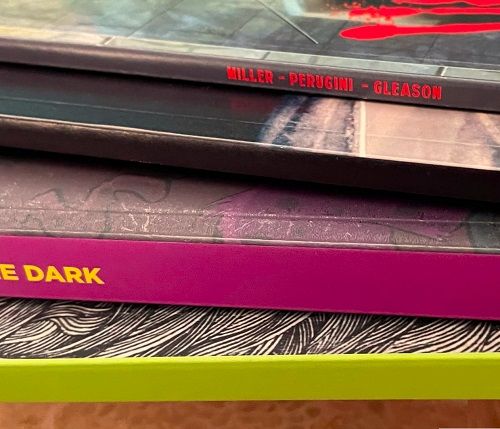
After the page block has been assembled, the spinal edge is
notched or "roughed up" using a machine with rotating blades. These
sharp blades expose more paper fibers, thus providing additional surface area for
the adhesive to make a stronger bond.
By this point in the process, the cover of the comic book
will have already been printed. Depending on the specs of the project, the
book's cover may have also received a durable clear coat, spot UV, or other
enhancements. The cover will also have been scored and creased so it will fit snugly
around the page block.
Once the page block and cover have been prepared, hot-melt
adhesive is applied along the spinal edge of the page block. The block is then
affixed to the center of the inside cover. Next, the cover is wrapped tightly around
the page block.
Once the glue cures, the comic book undergoes a trimming
operation. The three open sides of the book are trimmed to ensure the pages are
uniformly straight. These arrow-straight edges are where "perfect
binding" gets its name.
Whereas saddle-stitch binding is well-suited for comic books
with lower page counts, perfect binding is ideal for comic books and graphic
novels with medium to high page counts. In fact, the perfect binding method is not
recommended for books thinner than .125". This is because the glue needs
a bonding surface of at least .125" in width to ensure strong adhesion.
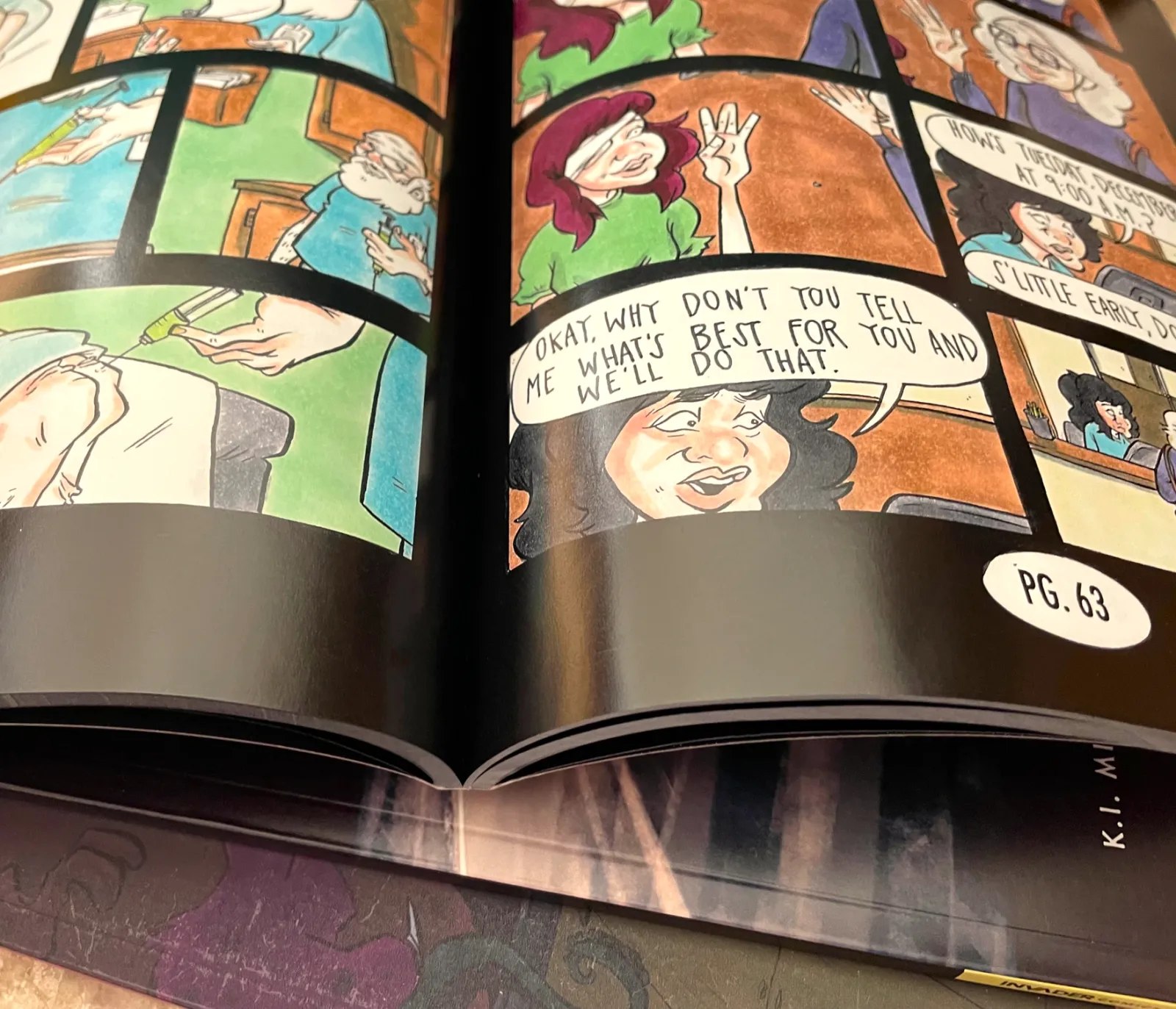
A big advantage of perfect binding is that it produces a
square spine. The flat surface of the spine allows for printing, such as the
comic book's title, author(s), volume number, etc.
Another benefit of perfect bound books is that they can stand upright in a bookcase or be stacked neatly on a shelf. Either way, the books can be easily
identified by the printing on the spine.
As far as cost is concerned, perfect bound books are not
quite as cheap as saddle-stitched books but they are still very affordable. Also,
the square, printable spine and crisp edges help to enhance the value.
Color Vision is always here to assist you!
Color Vision Printing has developed a strong reputation for producing
high-quality comics. As a full-service print facility, we have both digital and
offset production capabilities. This allows us to meet the needs of independent
creators as well as publishers. We also offer a wide variety of finishing and binding
options.
Just give us a call at 800-543-6299 to discuss your
project. Or, use our simple Quote Request form to send us your specs and we'll be
happy to email a custom quote to you.
By the way, Color Vision uses Polyurethane Reactive (PUR) adhesive
for all perfect bound projects. PUR is vastly superior to Ethylene Vinyl Acetate
(EVA) adhesive. PUR not only has superior adhesion and flexibility, it also offers
greater resistance to page pull-out and won't become brittle or crack.
As always, we look forward to assisting with
your next comic book or graphic novel. Just let us know how we can help!
Color Vision would like to thank INVADER COMICS for allowing us to display photos of their artistic works. As their print partner, we've always admired INVADER's passion for creating imaginative storylines and adventurous characters. All images within this article are used with their permission.
Related Articles
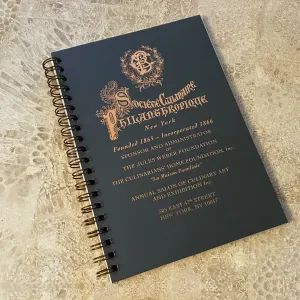
Is Wire-O Binding a Good Fit for your Custom Book Project?
Read This Article
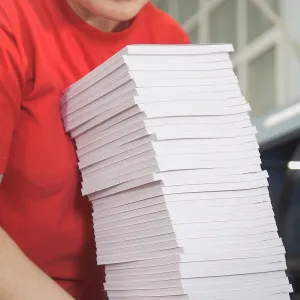
Book Printing Costs: How Order Quantity Affects the Price
Read This Article
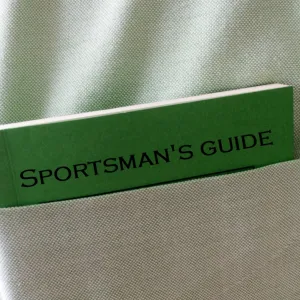
Pocket Size Book Printing: 9 Ways to Improve your Small Book
Read This Article
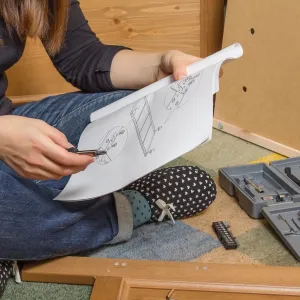
10 Ways to Reduce Printing Costs for Instruction Booklets
Read This Article